水泥厂稀油站控制系统的改造
一 稀油站的工作原理
稀油站的工作原理基本相同:油液由齿轮泵从油箱中吸出,经单向阀、双筒网式过滤器、换热器,被直接送到设备润滑点。每台稀油站设有2台油泵,一台工作,一台备用。稀油站油泵输出油压为0.4MPa,流量为2.5L/h。
润滑油流程:工作油泵一单向阀一过滤器一冷凝器(夏季使用)一压力继电器一主机设备润滑点一返回油箱—油泵。
二 稀油站控制存在的问题
1)电气控制回路复杂,中间继电器较多(共6个),故障率高,且问题查找及处理极为困难。
2)控制方式落后,2台油泵电动机的主、辅切换必须在现场进行,不能实现中控操作;现场岗位人员少,设备多,经常因出现问题发现不及时,而造成主机设备受损,影响生产。
3)稀油站通过压力继电器测量管路上的油压,来反映设备的润滑情况,这种方式灵敏度、准确度较差,很难保证可靠的润滑监测。稀油站的润滑状况监测方式一是压力继电器,二是压力变送器。两者都存在一定问题。
①在油路堵塞的情况下,油管压力仍然很高,但润滑油没有正常流动,设备得不到润滑。而对润滑状况的监测是判断出油管内的压力是否小于设定值,所以监测回路仍指示正常。改造前因稀油站压力继电器不能准确反映润滑状况,造成石灰石破碎的板喂机的减速机和水泥磨机轴瓦烧坏。
②主机设备的润滑部位(轴瓦或减速机)与稀油站油箱保持一定落差,以保证润滑油能顺畅地返回到稀油站的油箱中,这就使得淋油管端口与油箱也有一定的落差,且油泵出口管路中装有单向阀,防止回油。所以,即使一旦油泵停止工作,管路中润滑油仍存在一定静压,甚至超过压力继电器的设定值。
③润滑设备淋油处的油管端口的大小,也直接影响管路的油压值,造成对压力大小的错误判断。
④压力继电器提供的是开关量,无法在中控实现压力值显示,只能报警或停车,不能提前预制出应急措施。
三 改造方案
我们经过考察和论证,将其由监测油管压力改成监测流量的方式,即在油路中加一个流量变送器,监测润滑油的流量。不论是油管出口的大小、堵塞、管路的静压,或电动机转而油泵不打油,只要有流量即能满足润滑条件。
3.1流量变送器代替原电接点压力表
选用差动电容式流量变送器,它采用差动电容作为监测元件,整个变送无机械传动、调整装置,并且测量部分采用全封闭焊接的固体结构。因此仪表结构简单,性能稳定、可靠,且具有较高的精度。差动电容式流量变送器测量的是变化的压力,即输入差压Δpi.只有液态油在流动时才能作用于测量部件的感压膜片上,使其产生位移,从而使感压膜片(即可动电极)与两固定电极所组成的差动电容之电容量发生变化。此电容变化量由电容一电流转换电路转换成直流电流信号,电流信号与调零信号的代数和同反馈型号进行比较,其差值送入放大电路,经放大得到整机的输出电流I○(标准4~20mA),用于中控室画面显示和控制。
静压是不会产生差动压力的,所以避免了压力变送器对管路阻塞后的静压误认为是正常润滑的现象。
3.2 DCS程序控制取代原复杂的中间继电器
现场所有稀油站的电气控制全部改造为DCS程序控制,完全实现了主、辅油泵电动机切换的中控室集中控制和过程压力显示,并使控制回路简单化,大大降低了故障率,保证了主机设备的正常润滑。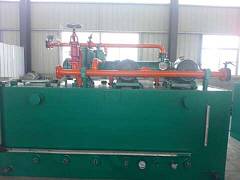
稀油站的工作原理基本相同:油液由齿轮泵从油箱中吸出,经单向阀、双筒网式过滤器、换热器,被直接送到设备润滑点。每台稀油站设有2台油泵,一台工作,一台备用。稀油站油泵输出油压为0.4MPa,流量为2.5L/h。
润滑油流程:工作油泵一单向阀一过滤器一冷凝器(夏季使用)一压力继电器一主机设备润滑点一返回油箱—油泵。
二 稀油站控制存在的问题
1)电气控制回路复杂,中间继电器较多(共6个),故障率高,且问题查找及处理极为困难。
2)控制方式落后,2台油泵电动机的主、辅切换必须在现场进行,不能实现中控操作;现场岗位人员少,设备多,经常因出现问题发现不及时,而造成主机设备受损,影响生产。
3)稀油站通过压力继电器测量管路上的油压,来反映设备的润滑情况,这种方式灵敏度、准确度较差,很难保证可靠的润滑监测。稀油站的润滑状况监测方式一是压力继电器,二是压力变送器。两者都存在一定问题。
①在油路堵塞的情况下,油管压力仍然很高,但润滑油没有正常流动,设备得不到润滑。而对润滑状况的监测是判断出油管内的压力是否小于设定值,所以监测回路仍指示正常。改造前因稀油站压力继电器不能准确反映润滑状况,造成石灰石破碎的板喂机的减速机和水泥磨机轴瓦烧坏。
②主机设备的润滑部位(轴瓦或减速机)与稀油站油箱保持一定落差,以保证润滑油能顺畅地返回到稀油站的油箱中,这就使得淋油管端口与油箱也有一定的落差,且油泵出口管路中装有单向阀,防止回油。所以,即使一旦油泵停止工作,管路中润滑油仍存在一定静压,甚至超过压力继电器的设定值。
③润滑设备淋油处的油管端口的大小,也直接影响管路的油压值,造成对压力大小的错误判断。
④压力继电器提供的是开关量,无法在中控实现压力值显示,只能报警或停车,不能提前预制出应急措施。
三 改造方案
我们经过考察和论证,将其由监测油管压力改成监测流量的方式,即在油路中加一个流量变送器,监测润滑油的流量。不论是油管出口的大小、堵塞、管路的静压,或电动机转而油泵不打油,只要有流量即能满足润滑条件。
3.1流量变送器代替原电接点压力表
选用差动电容式流量变送器,它采用差动电容作为监测元件,整个变送无机械传动、调整装置,并且测量部分采用全封闭焊接的固体结构。因此仪表结构简单,性能稳定、可靠,且具有较高的精度。差动电容式流量变送器测量的是变化的压力,即输入差压Δpi.只有液态油在流动时才能作用于测量部件的感压膜片上,使其产生位移,从而使感压膜片(即可动电极)与两固定电极所组成的差动电容之电容量发生变化。此电容变化量由电容一电流转换电路转换成直流电流信号,电流信号与调零信号的代数和同反馈型号进行比较,其差值送入放大电路,经放大得到整机的输出电流I○(标准4~20mA),用于中控室画面显示和控制。
静压是不会产生差动压力的,所以避免了压力变送器对管路阻塞后的静压误认为是正常润滑的现象。
3.2 DCS程序控制取代原复杂的中间继电器
现场所有稀油站的电气控制全部改造为DCS程序控制,完全实现了主、辅油泵电动机切换的中控室集中控制和过程压力显示,并使控制回路简单化,大大降低了故障率,保证了主机设备的正常润滑。
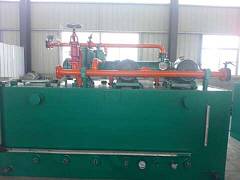